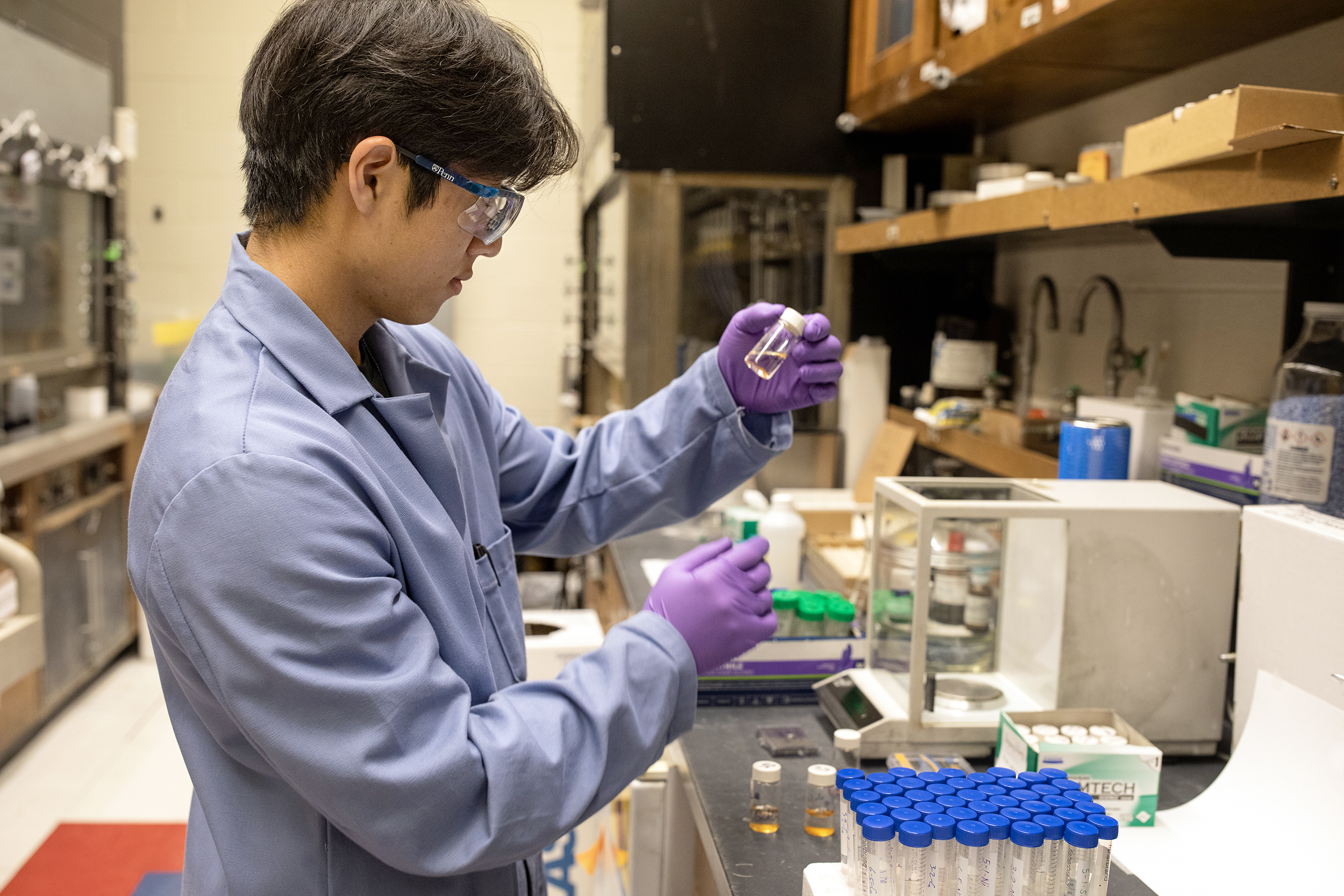
Sophomore Andrew Ahn, C’26, ENG’26, has worked on cars with his dad since childhood. His work this summer—which he hopes to continue—allowed him to marry that passion with those he has for chemistry and mechanical engineering, his two majors.
Tuesday, September 26, 2023
By Laura Dattaro
Images by Brooke Sietinsons
Scattered throughout the lab of chemistry professor Eric Schelter—under a box, on top of a shelf, in a drawer—are vials containing solutions of an orange cobalt compound powder that Andrew Ahn, C’26, ENG’26, left behind at the end of his summer research program.
But Ahn didn’t abandon his equipment. The powder is an essential part of a process to extract pure cobalt and nickel from the jumble of materials created when a car battery gets recycled or metals are mined from the Earth. He is crossing his fingers that the cobalt compounds in at least one of those scattered vials will crystallize, allowing him and his labmates to better understand the compound’s chemical structure.
Ahn, who is double majoring in chemistry and mechanical engineering, spent the summer in the Schelter Lab as part of his participation in the Vagelos Integrated Program in Energy Research (VIPER). By testing different concentrations of metals and solutions, Ahn helped improve a chemical process that could reduce the environmental harm associated with the lithium-ion batteries expected to power a more electric future.
Ahn’s drive for sustainability research derived from his lifelong love of cars; he has worked on them with his dad, a fellow auto aficionado, since childhood. In high school, as he learned about the ways that cars contribute to climate change, he realized that despite his love of engines, hybrid and electric cars were undoubtedly an important part of the automobile’s future.
“That realization got me to really look into sustainability,” Ahn says. “If we want to keep driving cars around, it’s crucial that we limit their climate impact.”
In 2021, the summer before his senior year of high school, Ahn participated in a research program at Stony Brook University. When he heard VIPER managing director Michelle Hutchings speak to the students in the program, Ahn decided he’d found his next step and applied early decision.
In a seminar for VIPER students this past spring, he heard Schelter speak about his lab’s work finding more sustainable ways to obtain metals used in electronics, like the lithium-ion batteries in hybrid or electric cars. The processes to extract those metals are not well developed, Schelter says, particularly because so many of the technologies that utilize them, including solar panels and wind turbines, are relatively new. The mining process is often environmentally destructive and can create economic structures that exploit local communities.
If we want to keep driving cars around, it’s crucial that we limit their climate impact.
“If you could enable local people with better chemistry that would allow them to produce a product that the rest of the world needs without doing widespread environmental harm and provide a good standard of living,” Schelter says, “that would be the ideal across the board.”
In Schelter’s work, Ahn found a union of his interests: hands-on research that could directly contribute to making cars more environmentally sustainable. In March, around the time Ahn was exploring options for labs to join, Schelter filed for a patent on his process for refining cobalt and nickel, bringing it one step closer to real-world use.
The two metals are often intermingled in ores extracted from the ground, and they react similarly to many chemicals, making them difficult to separate. The process usually requires solvents to dissolve the metals, and additional chemicals to extract each metal from the resulting soup. It can be expensive, wasteful, and environmentally harmful, Ahn says.
But last year, one of Schelter’s postdoctoral researchers discovered that when cobalt forms a particular compound (called hexamine cobalt chloride) and then comes into contact with a salt containing carbonate ions, the resulting complex becomes solid in solution. When the same process is applied to nickel, however, it remains dissolved, allowing the cobalt to be filtered out.
When Ahn joined the lab, he paired up with Boyang “Bobby” Zhang, a third-year Ph.D. student working to optimize the method to efficiently extract the purest cobalt and nickel in the highest possible quantities. Halfway through the summer, Schelter brought up an idea that gave the project new purpose: Could the reaction be used to improve recycling of lithium-ion batteries?
Only about 5 percent of such batteries are recycled each year, according to the American Chemical Society. That’s partly because mining new materials is cheaper than recycling them, Ahn says. “If we’re able to make the recycling process cheaper, if you’re able to make it faster or more efficient, you can promote battery recycling.”
To that point, Ahn and Zhang had largely been testing the reaction using pure lab chemicals. But during the recycling process, batteries get crushed into a jumbled conglomeration of metals and other materials called “black mass,” a more difficult but also more real-world test for their reaction. Unlike lab samples, black mass can’t be bought in a store. So, Ahn began tracking down places that might be willing to sell them black mass they could use in the lab.
“We want to attempt to use our method on these bona fide, real-world materials and see if it would still hold up,” Zhang says, “and if it doesn’t, what kind of improvements we need to make in order to achieve that.”
Beyond helping find black mass, Ahn made important contributions toward that goal, Zhang says. One day, the pair ran a reaction three separate times but kept failing to extract solid cobalt. They spent hours trying to figure out the problem. At the end of the day, Ahn suggested several potentially disruptive factors, Zhang says. They hypothesized that, since their hydrogen-peroxide solution was 70 percent water, it could have dissolved the cobalt.
“I’m glad that he got to experience both sides of the life of being a researcher, where sometimes it can be disappointing and even frustrating, but when it works it can be the best day,” Zhang says.
Ahn plans to return to Schelter’s lab next summer. In the meantime, he’s helping to write up a paper describing the work thus far. And, he says, his exposure to inorganic and organometallic chemistry—classes students usually take later in their academic careers—has given him a head start. “Looking into this has been pretty exciting,” Ahn says.
Motivating him throughout the summer was a sense that solving even seemingly small lab problems, such as coaxing cobalt compounds to crystallize, could lead to an end product with real-world impact in the near future. “I can see real applications for what I’m doing here,” Ahn says.